-
Course Code
SCLM-006
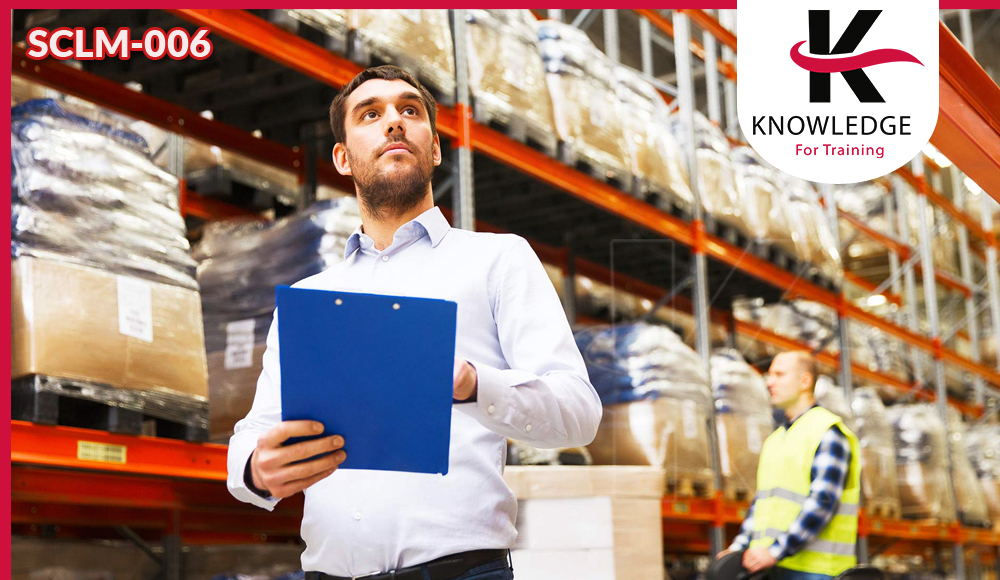
Warehouse Operations and Management
- You need a good warehouse to store, keep and protect all those millions of dollars. In this course, we will discuss the best and the latest methods to store and protect high value inventories. We will also discuss the best characteristics of a modern warehouse. Knowing what you have and how much you have are the keys to proper warehousing management. We will explore the various methods to achieve record accuracy and successful cycle counting. A scientific method of auditing the warehouse will be applied.
Learning Outcomes
- Maximize customer service and provide fast and accurate issuing
- Perform ABC inventory classification and cycle counting and calculate record accuracy and discrepancies
- Plan and control the warehousing operation to Minimize the operational costs.
- Guarantee safety to the warehouse personnel and facilities.
- Plan to develop the warehouse personnel
- Improve supervisory skills and deal more effectively with warehouse staff issues
- Effectively organize your store and warehouse
- Reduce time wasted in locating stock
- Use correct handling equipment
- Increase your knowledge on good housekeeping of store & warehousing functions
- Select the appropriate type of equipment
Course Contents
- Why we need a warehouse?
- What functions they cover?
- How do they fit into the supply chain?
- The balance between sorting and storing
- 12 initial questions to ask about warehousing activity
- Supply /demand variables
- ABC Analysis or the 80/20 rule
- Determining product handling groups
- Throughputs and product formats
- Receiving options
- Storage options
- Picking/assembly options
- Dispatching options
- Using the floor and the height space
- Organizing for flow
- Warehouse structures
- Loading bays
- Selecting forklift trucks
- Selecting racking
- Implications for warehouse layouts
- Operational timings and planning
- Duty of care
- Inspections and risk assessments-task analysis
- Equipment maintenance and care
- Raising people's awareness
- Minimizing internal theft
- Minimizing external theft
- Preventative measures will be briefly discussed
- Fixed and variable cost
- Typical costs involved
- A model for understanding the roles of productivity, utilization, and performance
- Setting productivity and cost targets
- The importance of having measurements and key indications of performance
- Internal and external customers
- The three key customer service measure
- Customer service sampling
- Effects of substandard service
- Minimizing errors
- Different methods
- Understanding of all involved
- Checklists to help on deciding the best option
- Separation of powers
- Legal issues
- How do we get inaccuracies?
- Roles and responsibility
- Requirements
- Job Descriptions
- Authority levels
- Tolerances and approvals
The Role of the Warehouse
Product Classification
Layout Options
Methods and Equipment
Health and Safety
Security and Loss
Productivity and Costs
Service Levels
Stock Coding
Stock Recording
Stock Checking
Our Methodology
- Make coaching and monitoring innovative and using modern
- Media training also using on the go training by using interactive means and focusing on
- The exercises, practical applications and real situations study
- Live delivery method, instructor-led training
- Experienced consultant, trainers, and professional
- Qualified trainer with high-level experience
Attendance Reports
- Send daily attendance reports to training departments
- Send full attendance report to training dep. by the end of the course
- Attend 100 % from the course days also provide daily
- Issue attendance certificate for participant who attend minimum 80% from the course duration
Pre/Post Reports
- Pre- assessment before starting training
- Post assessment after finish training
- Full report for the deferent between Pre-& Post assessment
Who Should Attend
- Storekeepers
- Warehouse & Inventory managers
- Warehouse supervisors who wish to enhance their current skills in managing stores and warehouse.
- Logistics operations personnel
